Whether modified powder will agglomerate during the spray drying process primarily depends on the effectiveness of the modification process, the control of spray drying parameters, and the properties of the powder itself. The following analysis is provided from different perspectives:
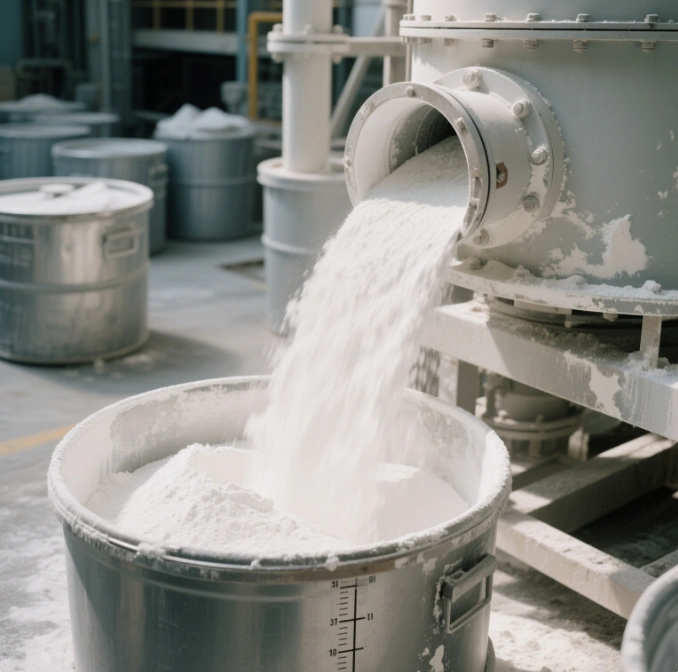
Functions and limitations of modifiers
Surfactants and coupling agents: By introducing surfactants (such as Tween 20, PVA) or coupling agents (such as silanes, titanates), the surface energy of the powder can be reduced. This reduces the van der Waals forces and hydrogen bonds between particles, thereby inhibiting agglomeration. For example, the modified powder may form uniform spherical particles (such as 3Y-B powder), significantly improving dispersibility.
Physical barrier and dispersion effect: Macromolecular modifiers (such as PEG) may form physical barriers during spray drying. However, if the dosage is too high or thermal decomposition is insufficient, it may cause particle adhesion or self-propagating reactions, aggravating agglomeration.
Effects and limitations of modifiers
Control of drying temperature and time
Temperature and time in spray drying are key factors that determine the final form of the powder. If the drying temperature is insufficient (below 180°C) or the residence time is too short, intermediate products may not fully decompose. These products may have strong hygroscopicity and are prone to forming hard agglomerates. Higher drying temperatures (280-480°C) and sufficient drying time (>5 seconds) help ensure complete drying of the particles. This reduces the risk of subsequent agglomeration.
Atomization effect and particle morphology
The atomization effect of spray drying directly influences the distribution range and shape of the particles. A good atomization effect, especially when using centrifugal nozzles, can produce spherical particles with a narrow particle size distribution and uniform shape. This helps reduce agglomeration. Additionally, the design of a countercurrent drying tower can enhance heat exchange efficiency. This improves drying efficiency and reduces the risk of particle adhesion.
Powder characteristics and post-processing
The particularity of nano-scale powders
Nano powders have extremely high specific surface areas. They are prone to moisture absorption and agglomeration. Even after surface modification, the powders still require additional physical dispersion methods, such as ultrasonic treatment or high-energy ball mill, to achieve lasting dispersion. However, these methods may only provide short-term dispersion effects. It is difficult to maintain the uniformity of the powders for a long time. Therefore, nanopowders usually require post-treatment after spray drying to ensure better dispersibility.
Necessity of post-treatment process
If the spray-dried powder needs further processing or use, it is typically subjected to high-temperature calcination treatment. For example, Al₂O₃ heat treatment is controlled between 1050-1250°C. Special attention must be given to temperature control during this process. Excessively high temperatures can cause particle sintering or secondary agglomeration. Appropriate post-treatment can improve the stability and dispersibility of the powder, preventing agglomeration.
Challenges in practical applications
Influence of Process Parameter Fluctuations
During production, if key parameters like feed rate, solid content, and blast speed are not properly controlled, uneven particle distribution or powder breakage may occur. This leads to agglomeration. For example, too fast a feed rate may result in larger particles. Similarly, too high a blast speed can cause uneven particle drying, leading to uneven distribution and further aggravating agglomeration.
Influence of Environmental Factors
Changes in ambient humidity affect the drying effect of powders. When humidity is high, powders that are not fully dried tend to absorb moisture. This forms soft agglomerates through liquid bridges. Additionally, ambient temperature and air flow also affect the efficiency of spray drying and the final powder form. To cope with these environmental factors, drying equipment operating conditions must be adjusted accordingly.
Conclusion
The modified powder may still agglomerate after spray drying. However, the risk can be significantly reduced with the following measures:
- Optimize the modifier: Select surfactants or coupling agents that are compatible with the powder. Control the amount added strictly.
- Precisely control drying parameters: Ensure that temperature, time, and atomization are matched to the powder characteristics.
- Combine with post-processing technology: Use heat treatment, ball milling, or surface coating (e.g., ALD technology) when it is necessary to enhance dispersion stability.
epic powder
Epic Powder, 20+ years of work experience in the ultrafine powder industry. Actively promote the future development of ultra-fine powder, focusing on crushing, grinding, classifying and modification process of ultra-fine powder. Contact us for a free consultation and customized solutions! Our expert team is dedicated to providing high-quality products and services to maximize the value of your powder processing. Epic Powder—Your Trusted Powder Processing Expert !